About
I am currently a Postdoctoral Scholar at Northwestern University in the Mechanical Engineering Department. I am working with Professor Wing Kam Liu. In the past I worked as a Research Engineer at Bridgestone Americas Technical Center at Akron, Ohio for three years designing, simulating, and testing tires. I graduated with a Ph.D. from Case Western Reserve University in the Mechanical and Aerospace Engineering Department in 2018. My advisers, Professor Michael Martens and Professor Ozan Akkus, are great human beings whom I try to imitate to my best. I am also honored to have Professor Robert Brown as one of my mentor. I am a member of OPTIMISE Lab and Tissue Fabrication and Mechanobiology lab at CWRU. My Current research aims at perfecting laser powder bed fusion additive manufacturing process. My developed FVM code helped us win four awards in the 2022 AM Bench Challenge held by National Institute of Standards and Technology. My PhD research work focused on non-linear multiphysics finite element analysis (FEA) of 1.5 T MgB2 based MRI magnet system at multiscale (micro and meso).
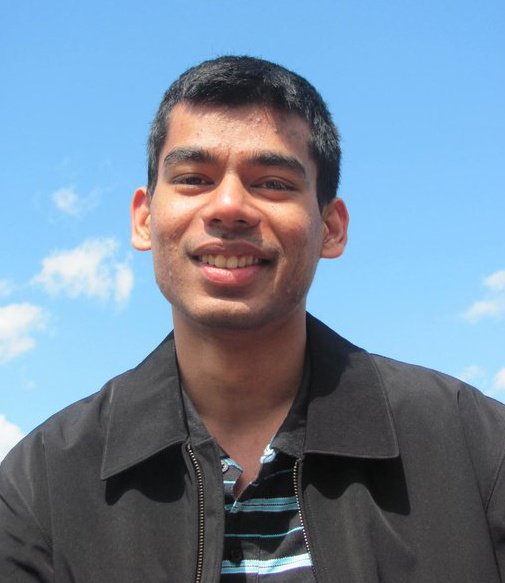
Postdoctoral Scholar, Northwestern University
Research Interest: Additive Manufacturing, Computational Mechanics, Superconducting Magnet, Multiscale and Multiphysics analysis.
- PhD, Mechanical and Aerospace Engineering, Case Western Reserve University 2018
- MS, Mechanical Engineering, The University of Akron 2014
- BS, Mechanical Engineering, Bangladesh University of Engineering & Technology 2009
Before coming to CWRU, I obtained my MS degree from the University of Akron. I have designed and developed a high throughput mircoparticle separation device based on inertial microfluidics using a Fermat spiral microchannel. Also, I completed the design and experimentation of a droplet microgripper device. My final goal of this research was to extend the capability of a microgripper to high temperature and vacuum application.
I obtained my BS degree in Mechanical Engineering from Bangladesh University of Engineering and Technology (BUET), the most prestigious university in Bangladesh. At my undergraduate class, I was involved in Robotics research. As part of the endeavor, I participated in an international robotics competition held at Pune, India in September 2008.
Facts
Some interesting facts!.
Article Published in peer reviewed Journals
Conference Proceedings scientific Meetings
Citations based on google scholar
h-index based on google scholar
Skills
My skills are derived from the years of experience through industry and academic research.
Resume
A detailed CV is available here and a brief resume is available here. A brief summary is provided below.
Sumary
Abdullah Al Amin
Postdoctoral Scholar, Department of Mechanical Engineering, Northwestern University, Evanston, IL.
Aiming to develop the next generation hybrid twin utilizing, novel multi-physics, multi-scale, reduced order computational modeling combining experimental data with the help of mechanistic deep learning methods.
Research Interests
- Additive Manufacturing
- Multiscale Multiphysics Modeling
- Computational Mechanics
- Computational Fluid Dynamics
- Scientific Deep Learning
- Mechanics Informed Neural Network
Education
Doctor of Philosophy
2013 - 2018
Case Western Reserve University, Cleveland, OH
Multiscale multiphysics computational modeling of full body MRI magnet systems
Master of Science
2010 - 2014
The University of Akron, Akron, OH
Inertial microparticle separation based on passive microfluidic forces.
Bachelor of Science
2004 - 2009
Bangladesh University of Engineering and Technology, Dhaka, Bangladesh
Design, Improvement, Modification & Fabrication of Mechanisms and Control Systems of Robots for ABU ROBOCON.
Research Experience
Postdoctoral Scholar
2021 - Present
Northwestern University, Evanston, IL
- Laser Powder Bed Fusion Addditive Manufacturing Process
- C++ FVM code development.
- Reduced Order Modeling
- Awardee of three 2022 NIST AM Bench Additive Manufacturing Competition
Research Engineer
2018 - 2021
Bridgestone America Technical Center, Akron, OH
- Designing and analysis of passenger and truck/bus radial tire.
- Tire test data fitting with Pacejka Model, MF Tyre, and FTire for vehicle analysis.
- Software development with python.
Graduate Research Assistant
2013 - 2017
Case Western Reserve University, Cleveland, OH
- Multiscale Modeling of a full body MgB2 based MRI magnet.
- Design of biomedical device design. (Co-Inventor to an awarded patent)
Graduate Research Assistant
2010 - 2013
The University of Akron, Akron, OH
- MEMS based microgripper design.
- Microparticle separation device based on passive microfluidics.
Publications (Selected)
Selected list of publication. Follow this link for full list of publications.
Metal Matrix Superconducting Composite Wire
Magnetic Resonance Imaging (MRI) background magnets are made from superconducting composite wires that are a metal matrix composite (MMC). Thermal and mechanical properties of the specific wire matrix must be known to optimize the wire configuration for MRI magnet designs. Computational analysis techniques based on numerical homogenization may provide an accurate characterization of a multifilament MMC wire and can reduce the expenses and time required for experimental tests.
Multiscale and multiphysics model of full body MRI magnet
High temperature superconductors such as MgB 2 focus on conduction cooling of electromagnets that eliminates the use of liquid helium. With the recent advances in the strain sustainability of MgB 2, a full body 1.5 T conduction cooled magnetic resonance imaging (MRI) magnet shows promise. In this article, a 36 filament MgB 2 superconducting wire is considered for a 1.5 T full-body MRI system and is analyzed in terms of strain development.
Atomistic study of perovskite solar cell
First-principles calculations were carried out to study the perovskite interfaces with TiO2, ZnO, and SnO2. Our study suggests that the binding energy of MAPI on SnO2 is weak compared to TiO2 and ZnO. However, we show that the strong binding to TiO2 and ZnO deprotonates CH3NH3 molecules which influences the decomposition process.
MEMS based soft microgripper for delicate object handling
Aqueous droplet-based micro-gripper has been used for micro-assembly for high temperature and vacuum applications. Ionic liquids, organic salts that have a lower melting point temperature, appear suitable for droplet-based micro-gripping application in high temperature and vacuum environments because of their nonvolatility and thermal stability. In this paper, we demonstrated the use of ionic liquid as the operating liquid for micro-gripping applications in high temperatures (up to 110 C) and vacuum (up to 24 inch Hg) environments.
Stochastic additive manufacturing simulation for roughness and porosity prediction
Deterministic computational modeling of laser powder bed fusion (LPBF) process fails to capture irregularities and roughness of the scan track, unless expensive powder-scale analysis is used. In this work we developed a stochastic computational modeling framework based on Markov Chain Monte Carlo (MCMC) capable of capturing the irregularities of LPBF scan.
Mechanical analysis of full body magnet construction..
The winding of composite superconducting wire around a mandrel is one of the first stages of manufacturing processes of a superconducting magnet. Depending on the method of mechanical support conditions during winding, the strain development at the final stage in a superconducting magnet may vary significantly.
Contact
Please reach out to me for exciting collaboration!.
Location:
2603 Ewing Avenue, Evanston, IL 60201
Email:
abdullah dot amin at northwestern dot edu
Call:
eight five seven two three one zero one nine eight